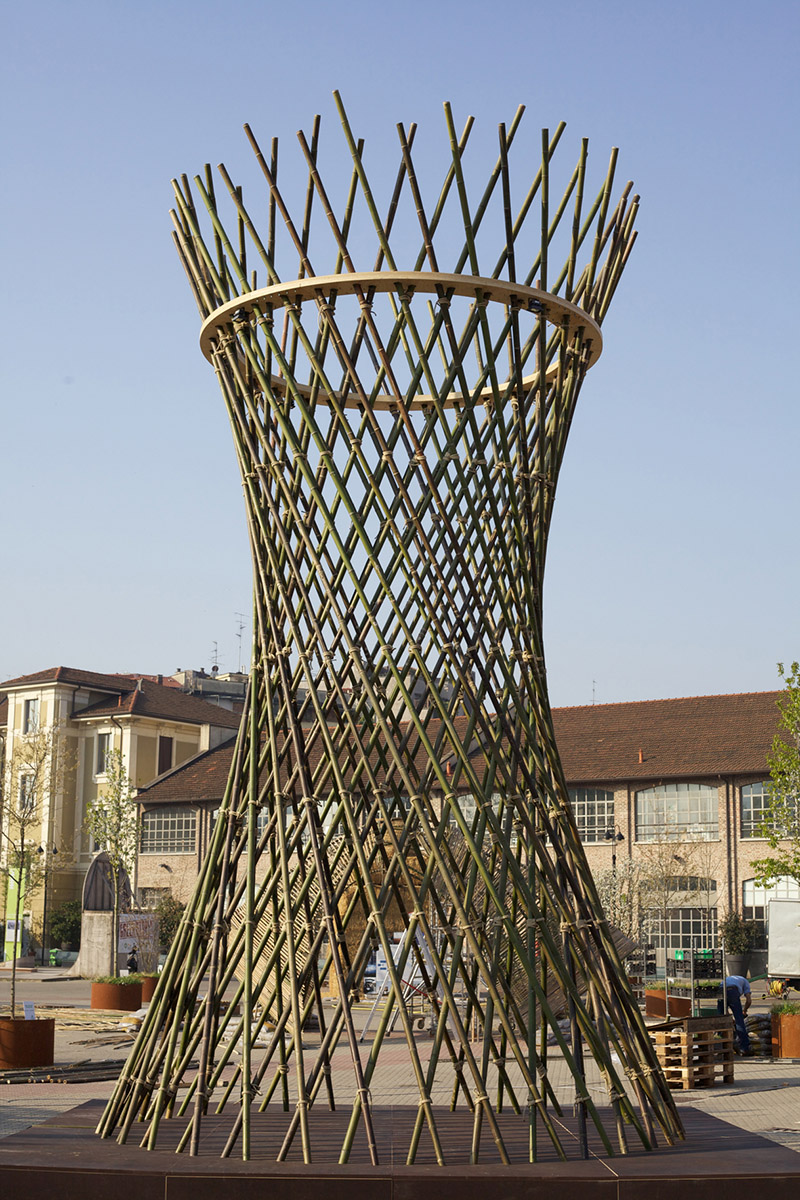
Keck recken sich 64 gekreuzte Bambusstäbe im Innenhof der Fabbrica del Vapore der Frühjahrssonne Oberitaliens entgegen.
Foto: Mafell/Daniela Friebel
Der filigrane Torre di Bambù (Bambus Turm) wird scheinbar nur von Seilen und einem Holzring in 6 m Höhe zusammengehalten. Die Besucher der Ausstellung Green Utopia in Mailand entdecken erst bei genauer Betrachtung, dass die Bambusstäbe passgenau in einem Sockel aus Konstruktionsvollholz stecken. Der Elektrowerkzeughersteller MAFELL hat das Team des renommierten Berliner Architektur- und Ingenieurbüros Ziegert I Roswag I Seiler mit Maschinen und Know-how bei der Erstellung der Holzkonstruktion und der Montage unterstützt.
Dieses Bauwerk war bis 8. Mai Eye-Catcher der Ausstellung Green Utopia im Rahmen der Mailänder Möbelmesse und soll anschließend einen Platz bei der EXPO in der lombardischen Metropole finden. Die Macher verstehen den 8 m hohen Bambus Turm zuvorderst nicht als Kunstwerk, sondern als Beweis, dass das schnell wachsende Gras längst nicht mehr nur Rohstoff für Bodenbeläge, Dekoratives, Gartenmöbel, Palisaden oder Terrassendielen ist, sondern auch konstruktives Baumaterial. Die Statiker des Büros haben zusammen mit der TU Berlin ein FEM-Modell entwickelt, das als Grundlage für den statischen Nachweis der Konstruktion dient. Nicht nur wegen der auftretenden Windlasten, sondern auch wegen der Verkehrslast von bis zu zehn Personen auf der noch zu installierenden Aussichtsplattform.
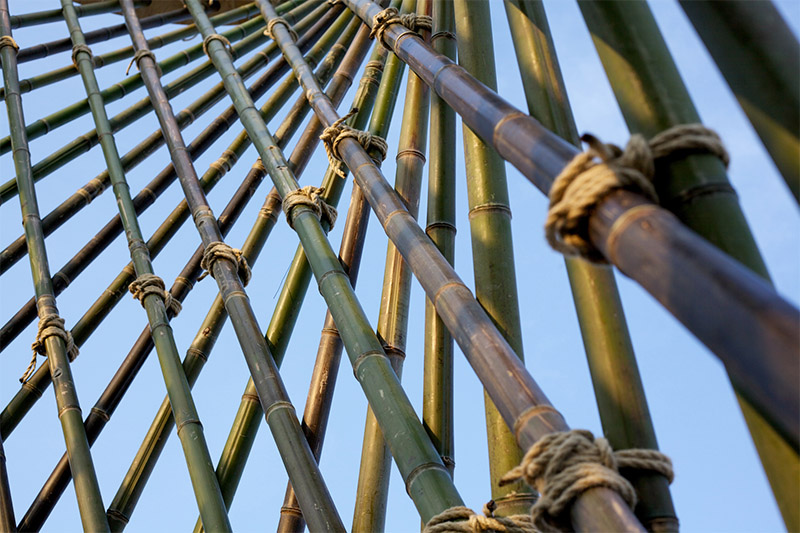
Der Bambus Turm vereint ästhetischen Anspruch mit statischen Anforderungen.
Foto: MAFELL/Daniela Friebel
Für das Team um die Geschäftsführer Eike Roswag und Uwe Seiler sowie den italienischen Projektpartnern und Bambusproduzenten bambuseto sind die Eigenschaften des Bambus keine neue Erkenntnis. Eike Roswag, der diesjährige Träger des renommierten KAIROS-Preises, hat bereits jahrelange Erfahrung mit dem Baustoff Bambus. In Zusammenarbeit mit Anna Heringer hat sein Büro unter anderem die weltweit mit Architekturpreisen ausgezeichnete METIschool in Bangladesch entworfen und das Tragwerk geplant.
„Der Bambus ist ein sehr nachhaltiger Baustoff, der längst nicht mehr aus Südostasien transportiert werden muss. Die Stangen für den Bambus Turm sind auf einer Plantage in der Toskana vergangenes Jahr geerntet worden“, erklärt Eike Roswag. Bald darauf entstanden die ersten Entwurfsskizzen, später ein 3-D-Modell zur statischen Berechnung und vor der Ausführung ein 1:5-Modell.
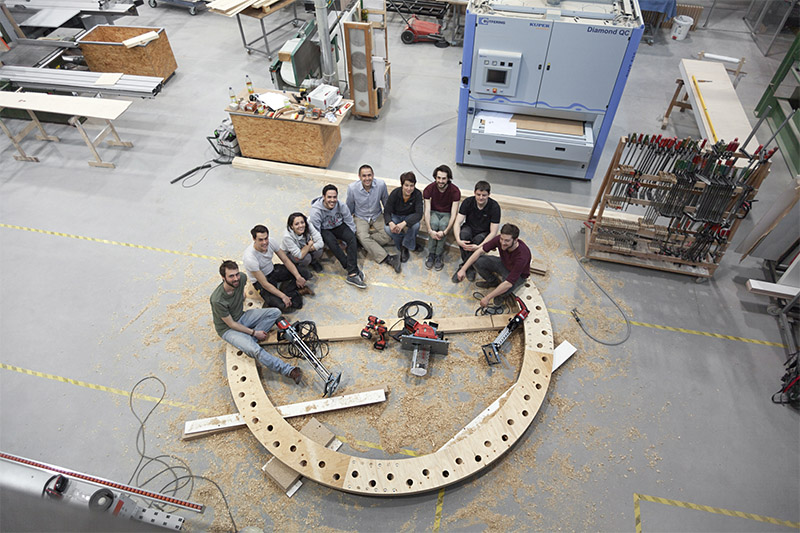
Innerhalb nur eines Tages hat das Team mit den MAFELL Zimmereimaschinen die Holzelemente für den Bambus Tower vorgefertigt.
Foto: MAFELL/Daniela Friebel
Die mit dem Baustoff Bambus versierten Mitarbeiter des Architektur- und Ingenieurbüros entwarfen eine filigrane Konstruktion mit schräg geneigten und sich kreuzenden Stangen, die im Sockel in einen Ring mit 4,70 m Durchmesser und himmelwärts auf Höhe der späteren Aussichtsplattform von einem 4,20 m im Durchmesser messenden Ring gefasst werden. In der Mitte verjüngt sich der Turm auf nur noch 2,60 m Durchmesser. Die besondere Geometrie des Bauwerks und die statische Belastung erforderten eine besonders haltbare und präzise Befestigung der Stäbe.
Dazu wurden in einem 6 x 6 m großen Podest ringförmig 16 Blöcke (32 x 20 cm) aus Konstruktionsvollholz angeordnet und exakt positioniert, Aufnahmebohrungen für die Stangen gesetzt. Bei der Auswahl der geeigneten Maschinen, Bohrer und Fräsköpfe haben die Experten von MAFELL die ambitionierten Turmbauer unterstützt. „Gerne haben wir für das Projekt Maschinen und Know-how bereitgestellt, da es für die Realisation besonders ausgefallener architektonischer Ideen auch besonders präzise Maschinen braucht“, erklärt Ralf Kohler, Leiter Gesamtvertrieb und Marketing bei MAFELL.
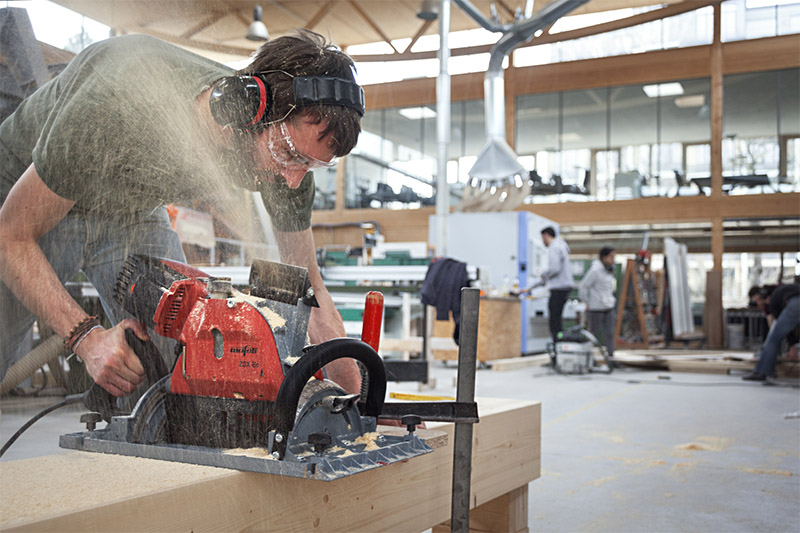
Foto: MAFELL/Daniela Friebel
Die Blöcke für die Aufnahme der Stangen und die Unterkonstruktion für das Podest wurden mit der MAFELL Kettensäge ZSX Ec 260 HM gesägt. „Die Schnittgeschwindigkeit und die Qualität des Schnittbildes sind beeindruckend“, meint Eike Roswag begeistert. Die Tischler von Artis Engineering unterstützten das Projekt unter anderem mit der Vorfertigung der Kisten für das Podest und das Fräsen des oberen Ringes. An nur einem Tag fertigte das neunköpfige Team die gesamte Holzkonstruktion. In die 16 Sockelblöcke und die vier Ringelemente für die Krone wurden mit der MAFELL Bohrmaschine HB 1 E mit dem Holzbohrer 16 x 460 mm insgesamt 128 Aufnahmen vorgebohrt. Der schwenkbare MAFELL Bohrständer BST 460 hat die exakte Bohrung mit einer Neigung von 24,7 % und die Tiefe von etwa 22 cm ermöglicht.
Das Konstruktionsprinzip des Bohrständers ist bislang einzigartig. Basis ist eine Profilsäule aus robustem Aluminium-Guss. Die Bohrmaschine wird direkt am Adapter der Säule eingespannt und über ein hochfestes Seil in einer Schiene geführt. Die Zugkraft des Seils kann individuell auf die Bohrerlänge eingestellt werden. Nach dem Bohren fährt die Maschine automatisch zurück. Dieses Einsäulen-Prinzip bietet bei der Arbeit entscheidende Vorteile. So lassen sich Anriss und Bohrerspitze besser einsehen, beim Bohrerwechsel steht mehr Platz zur Verfügung und ein Verkanten beim Bohren ist nicht mehr möglich.
Nicht nur die Führung der Bohrmaschine, sondern auch die Führung des Bohrers garantiert eine präzise Bohrung. Der Bohrer wird von sechs vertikal gelagerten Rollen geführt, die ein Verlaufen des Bohrers verhindern. In Kombination mit der schwenk- und justierbaren Säule gelingen so auch Schrägbohrungen in Balken. Die beiden schwenkbaren Modelle können zweiseitig über eine Skala von 0° bis 45º ausgerichtet werden. Drehpunkt ist immer die Bohrerspitze.
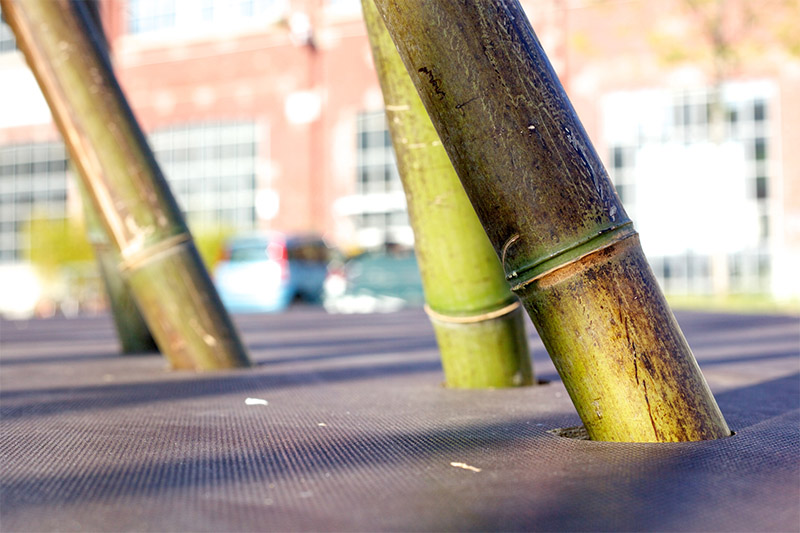
Die insgesamt 128 Bambusstangen wurden passgenau in die Aufnahmen eingesetzt.
Foto: MAFELL/Daniela Friebel
Die exakt vorgebohrten Löcher wurden mit einem 60 mm großen Kopfsenker mit der MAFELL Zimmereibohrmaschine ZB 400 E auf das Sollmaß aufgefräst. Die leistungsstarke Zimmereibohrmaschine mit Rechts- und Linkslauf konnte dazu exakt im Schwenkbereich von 0 bis 45° justiert werden.
Beim Aufbau in Mailand wurde das Podest mit beschichteten, 19 mm starken Siebdruckplatten verkleidet, im Inneren mit 1,5 t Sandsäcken beschwert, dann wurden die Stangen eingesetzt. Mit dem Handhobel wurden die 55 bis 60 mm starken Stangen für eine passgenaue Aufnahme bearbeitet.
Geduld und Übung waren gefragt bei der Verknotung der Stangen. Das Team hatte sich dazu von einem Zimmermann und Korbflechter in Berlin die Technik zeigen lassen und sich in Mailand mit einem Bambusgerüst von innen, Knoten um Knoten, nach oben gearbeitet – insgesamt 192 Mal.
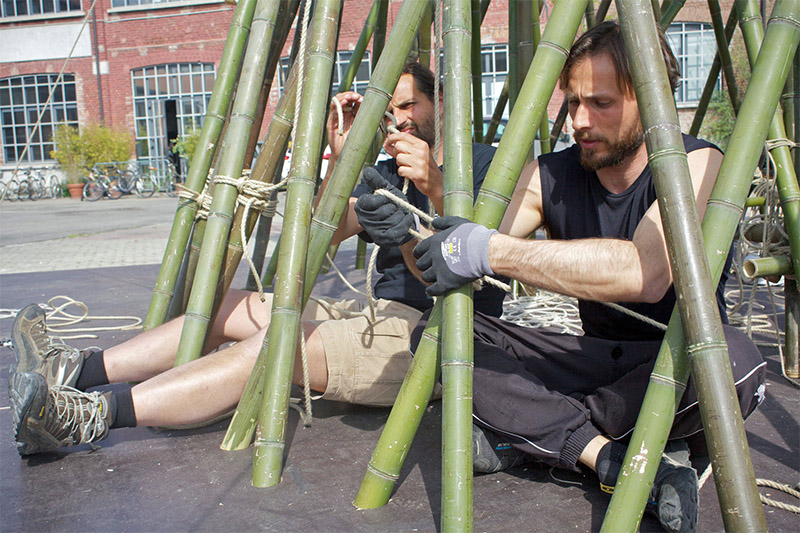
Das Team hat die sich kreuzenden Bambusstangen mit 192 Knoten fixiert.
Foto: MAFELL/Daniela Friebel
Nahezu unsichtbar im Flechtwerk bleiben dabei die Verbindungsstöße der Stangen. Um die Last statisch sicher und berechenbar einzuleiten, sind diese wie im Betonbau als Bewehrunganschluss ausgeführt. Dazu ist die Stange in der jeweils ersten Nodie (Knoten) mit Beton ausgegossen, in denen ein Gewindestab eingelassen ist.
